Why choose SENGA aluminium tubes for your compressed piping system?
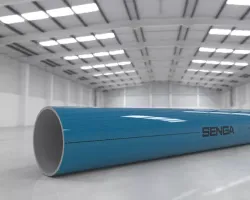
Pressure losses, money losses
The issue of pressure losses in galvanized steel compressed air networks is a major concern for many businesses using pneumatic systems. Galvanized steel, while widely used for its corrosion resistance, has characteristics that can lead to significant pressure losses in air ducts. The roughness on the inner surface of pipes, often present even in high-quality galvanized steel pipes, can create turbulence in the airflow, thereby increasing pressure losses. Additionally, bends, fittings, and other obstacles in the network can exacerbate this problem by creating additional restriction points. These pressure losses not only reduce the energy efficiency of the system by requiring higher air pressure to maintain the required flow rate but can also lead to decreased performance of pneumatic equipment, such as tools and machines. To address this issue, it is essential to adopt effective solutions for managing pressure losses, such as using smooth pipes and appropriate diameters, as well as minimizing bends and obstacles in network design. By investing in quality components and optimizing system design, businesses can reduce pressure losses, improve energy efficiency, and prolong the lifespan of their pneumatic equipment.
Most common causes of pressure losses:
- Undersized network: tube diameters too small for the application.
- Inadequate network structure: bends, changes in section increase pressure losses.
- Internal roughness of tubes: oxidation or unsuitable material (galvanized steel tubes, for example) will cause resistance to the passage of air.
- Malfunctioning air filters: non-homogeneous fluid undergoes a significant pressure drop.
Important: It is advisable not to exceed a pressure loss of 4% of the supply pressure of your air network.
Costs of a compressed air network over its lifespan: energy consumption (75%), maintenance (15%), and equipment/installation (10%).
As we inexorably move towards energy efficiency, saving on the quality and sizing of the equipment (pipes and fittings) used in your compressed air network is the worst possible calculation. The performance (energy efficiency) and lifespan of your compressed air network depend heavily on the quality of the tubes used. To address technical and economic challenges, the choice of aluminum tubes is essential. SENGA tubes (8300 series) are made of extruded aluminium alloy and coated with RAL 5012 paint. The inner walls have very low roughness, thereby reducing pressure losses. They will meet your expectations both in terms of installation and energy performance.
Galvanized Steel Tubes vs. Aluminum Tubes: A Clear Conclusion
Galvanised steel tubes:
High pressure losses (high roughness)
Risk of leakage
Risk of corrosion
Supplied without paint
Heavy tubes
Difficult to cut manually
Difficult to deburr
Rough and dirty surface

SENGA pipes in high quality aluminium:
Minimised pressure drop (divided by 2)
Low risk of leakage
Corrosion resistant
Tubes painted to RAL 5012 (compressed air)
Lightweight tubes
Quick and easy manual cutting
Fast deburring
Smooth and low dirt surface

Technical characteristics of SENGA pipes:
- Diameters: ø25 - ø40 mm (calibrated)
- Thickness: 1.5 mm
- Lengths: 3 or 6 m
- Material: Extruded aluminium alloy EN AW 6060-T6
- Colour: RAL 5012 (compressed air colour)
- Marking: SENGA
- Electrostatic paint (certified non-toxic according to UNI 9983)
- Coefficient of expansion: 0.024 mm/(m°C)
- Density: 2.70 kg/dm3
- Complies with Directive 97/23/EC art 3.3 (PED: Pressure Equipment Directive)
Conclusion
While using galvanized steel tubes may seem like an economical solution, it is far from the reality. Indeed, it entails several significant drawbacks that must be taken into consideration. The high roughness of galvanized steel leads to significant pressure losses, which can compromise system performance and result in increased energy costs. Additionally, their moderate lifespan and propensity for leaks and corrosion require regular maintenance and can lead to costly production interruptions. The fact that these tubes are supplied unpainted makes them more vulnerable to environmental damage, while their heavy weight and difficulty in handling make installation laborious. Manual cutting and deburring of these tubes are also challenging and potentially hazardous tasks, adding further challenges to their handling. Furthermore, their rough and dirty surface increases the risk of contamination and pollution of compressed air, which can compromise air quality and industrial process safety. Considering these drawbacks, it is clear that galvanized steel tubes have significant limitations compared to other options available on the market. Using SENGA aluminum tubes will allow you to optimize the energy performance of your compressed air installation in the long term and thus save on your electricity bill (75% of the cost of a compressed air network over 10 years).
In conclusion, SENGA aluminum tubes prove to be a wise choice for compressed air networks, offering a combination of exceptional advantages. Their ability to minimize pressure losses, remarkable lifespan, corrosion resistance, and compliance with standards make them a reliable and durable option for any pneumatic installation. Additionally, their lightweight, ease of cutting and deburring, as well as their smooth and less dirty surface, contribute to simplifying installation and ensuring long-term efficient operation. By investing in SENGA aluminum tubes, companies can not only optimize the performance of their compressed air systems but also reduce maintenance costs and improve overall productivity.